THE CHALLENGES OF CREATING CLEAN WORKING ENVIRONMENTS
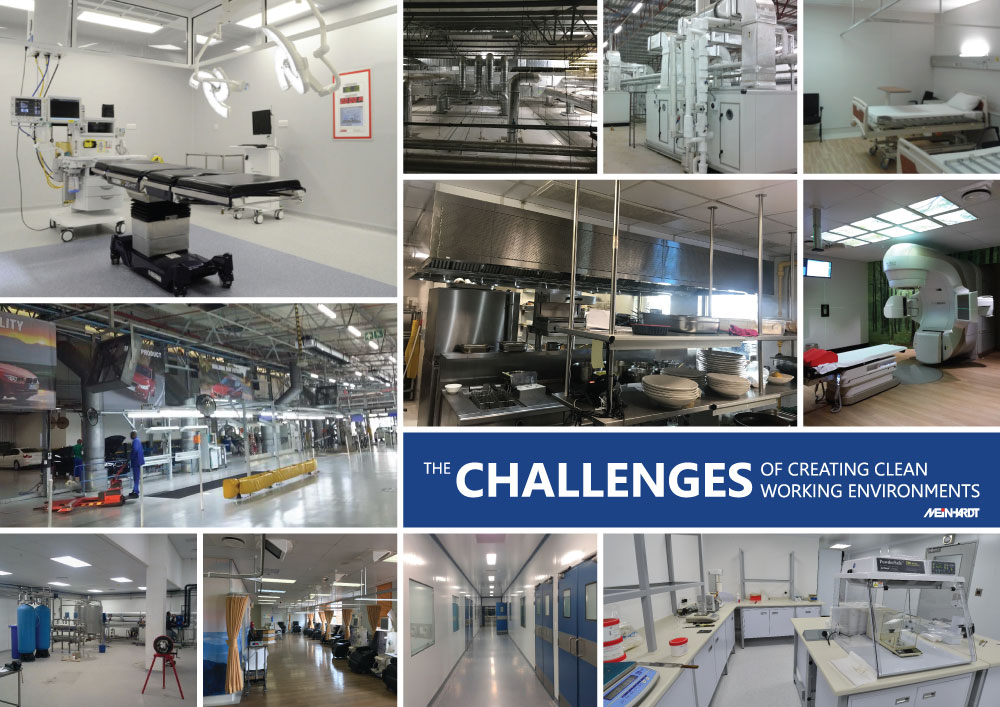
With the CORONAVIRUS epidemic spreading from China across the globe and the WHO declaring it a global health emergency on Thursday, 30 January 2020, maybe it is time to talk about CLEAN ENVIRONMENTS and the role that we as MEP Design Engineers play to create and maintain these environments. People wearing masks in response to this crisis has become common sight, though, in the light of their insufficient protection it is important to expound on the controlled environments that Good Engineering Practices (GEPs) can provide for further safeguarding.
REMEMBER: Sick People concentrate in clinics and hospitals, so these are the facilities to be very cautious of upon entering in times such as these.
NOTE: Large open spaces or areas with high ceilings are the safer places to be.
BACKGROUND
All the way from offices to kitchens to workshops to hospitals to pharmaceutical manufacturing, design teams are challenged to create CLEAN WORKING ENVIRONMENTS to safeguard employees as they go about their work.
In all these areas the responsibility lies with the Architects and then the HVAC Engineers and Contractors to install and maintain installations and equipment that will GUARANTEE these clean environments so that we can keep our people safe and healthy.
In the HVAC and Cleanrooms industries there is a lot of legislations in place on what rules/design standards to follow (such as WHO and CDC and ASHRAE), but the challenge is always to design something that is practical and that can be successfully maintained; as well as to use equipment that does not use too much energy as they will just be bypassed when the high maintenance and electricity bills starts coming in.
DEFINITION OF A “CLEANROOM” or CLEAN ENVIRONMENT
Wikipedia defines a Cleanroom in the following manner:
A facility ordinarily utilized as a part of specialized industrial production or scientific research, including the manufacture of pharmaceutical items, integrated circuits, CRT, LCD, OLED and microLED displays. Cleanrooms are designed to maintain extremely low levels of particulates, such as dust, airborne organisms, or vaporized particles.
This means that a CLEAN ENVIRONMENT is a place where the amount of dust and bacteria is removed from the airstream or the air in circulation and thus the resultant “dirt” that settles on mostly horizontal surfaces is kept as low as possible.
Bacteria and Viruses also tends to attach or cleave to dust particles – so the less dust particles you have in the air, the lower the amount of likely bacteria is in the air.
To get slightly more technical, let us quickly list the Cleanroom Classes and what they mean:
- ISO Class 9: This is considered “Unclassified Clean” or just a clean area like ICU at a hospital, etc.
- ISO Class 8 (GMP Grade D): From here on there are Hepa Filters involved and it usually refers to the general areas in pharmaceutical plants.
- ISO Class 7 (GMP Grade C): This is typically a hospital theatre and referred to as a “sterile area”.
- ISO Class 6 (GMP Grade C/B): This is typically a more specialized theatre (such as an open-heart surgery procedure room) or certain medicine filling/mixing areas in pharmaceutical plants.
- ISO Class 5 (GMP Grade A): This is where sterile filling for IV injectables would typically take place.
- ISO Class 4-1: This relates to microchip manufacturing areas.
- BSL 1-4: This refers to the most highly controlled environments where biosafety and bacterial classes are involved and typically refers to specialized research laboratories or isolation areas.
DEFINING A DIRTY ENVIRONMENT
In light of the preceding section, a dirty area is thus an area where the dust and possible contaminated air flows freely without any filtration and so also, obviously, an area where you have dirty surfaces. A building with open windows for fresh air is therefore a slave to the “Air Quality” outside, so on a dusty day the inside air will represent the same quality and the environment is not controlled.
HAVING THE CORRECT ENVIRONMENT OR FINISHES
The architect, or more specifically the internal designers, plays a big role when specifying the finishes inside any room or area where you want to create a clean environment and in turn effects the success of controlling the environment heavily.
Any form of surface (particularly horizontal) that you cannot properly access is a potential place where dust or bacteria can accumulate and grow – so washable walls, floors, ceilings, windowsills, etc. and the material that they are made off is critical.
If you compare a carpeted floor to a neatly tiled or epoxy floor, it is obvious which one can be kept more hygienic. Moreover, carpets and curtains even create its own dust which is deposited into the airflow and also stores bacteria for long periods where they can grow.
The playoff here is between bad acoustics and bad air quality, and the two often stands diametrically opposed.
CHOOSING THE CORRECT LAYOUT DESIGN
In a pharmaceutical plant or hospital Standard Operating Procedures (SOP’s) are developed for the staff to make sure that everybody working inside these areas follows the correct procedures, enter and leave from specific areas and wears the correct clothing etc.
The best way to ensure environments stays controlled is to design the layout of the facility and access control in such a way that the doors and rooms “forces” you to follow the correct procedures and routes. This also is true for kitchens and laboratories (and even office environments), and again the internal designer or Architect plays an important role here.
The simple practice of just drawing a RED LINE across the floor where two zones comes together makes people think before they “cross the line”.
THE DIRTY AND EXPENSIVE FRESH AIR (FA) DILEMMA
The Fresh Air (FA) supply to a building or facility is specified or controlled by legislation and is “normally” part of the original design (granted the facility has been designed for its current purpose by a competent HVAC engineer).
The amount of FA added to a facility is normally defined by the type of area or volume involved and is calculated as a % of the volume or airflow, or more specifically the AIR CHANGES that takes place, and can be defined as 100% if Bacteria plays a big role.
Testing the amount of CO2 in the air is a very practical way of determining if you have enough FA coming into an occupied area where people work.
AIR CHANGES is the amount of times that the volume of air inside an area is replaced per hour by the HVAC or Aircon system and is 10x for an office, starts at 20x for an ISO-8 areas and goes as high as 350x for an ISO-5 area, and then the directional flow of the air is critical.
The DILEMMA with FA is that it can be DIRTY so it needs filtration to certain standards and it is EXPENSIVE in the manner that it adds a lot of load to the Aircon System – so the common workaround is to just switch it off to save energy or maintenance.
In Thailand where there is very high humidity, the use of FA can be very challenging and expensive and the prevalence of switching off the FA systems for energy saving is very common. Also in a lot of places where FA legislations is not enforced it is just ignored.
The sight of dirty diffusers or aircon outlets in office spaces is a common sight and a direct indication of the condition of the air.
THE MYTH OF ADDING EXHAUST SYSTEMS
A common scene found in workshops, toilets, kitchens or labs is a situation where more and more EXHAUST SYSTEMS were just added over the years with no real plan or design.
The argument goes: If you have a smelly or dirty or dusty area – just add another extract system.
The common problem is that those extract systems were not part of the original air balance design and the HVAC Engineer is long gone and not part of the solution.
Extracting air from a room or a volume creates a VACUUM so that air must come from somewhere – and that is normally uncontrolled.
One of the biggest culprits here is KITCHEN EXTRACT HOODS and mostly in takeaway shops where you have a cooking area with a very small shop in front and no air makeup system to supply the amount of air being extracted from that kitchen.
In TB Wards or Isolation wards the “directional airstream” is crucial so YES a properly designed Extract System is effective or even crucial.
CAN YOU KILL THE VIRUS?
The only way to “kill” viruses is the use of UVGI lights, but the problem is that these lights pose a danger to your eyes so they cannot be placed in open spaces or in direct view.
In TB Facilities they are sometimes placed in a higher ceiling void above the people with grids to protect your eyes, but the air must flow slowly (dwell time) past these lights, so it is very difficult to control.
UVGI Lights loses effectiveness over time so they need to be tested regularly for effectiveness.
Bacteria or Viruses cannot be FILTERED from the airstream and they can even get stuck in the filter systems to spread at a later stage. Luckily viruses needs a host with heat and moisture to survive so they die after a while in cool dry areas or if they float up un the air and gets exposed to sunlight.
Bacteria can be “tested” or traced by doing swap test samples on surfaces but to test for Bacteria or Viruses in the airstream is almost impossible and the existence of a Virus in a facility can only be tested by using Gini pique animals.
MAINTAINING THE ORIGINAL OR INTENDED DESIGN
Companies like Meinhardt employs professional engineers with years of experience in creating clean environments and designs facilities so as to navigate around the problems outlined above,
so it is always best to have your installation or facility designed by a professional team.
The use, intention or design of a facility often changes over time – so it is crucial to have your facilities checked or reviewed from time to time.
WHAT ABOUT NATURALLY VENTILATED AREAS?
If designed and controlled correctly, it is possible to create safe environments using natural ventilation.
The challenge, though, is to DESIGN or PREDICT the natural flow of the air in a newly/specially designed facility or building and the only successful method is the use of Computational Fluid Dynamics (CFD). A CFD Model uses powerful computers and is time consuming and expensive to compute. It involves a method whereby the layout of the building is repeatedly tweaked and analyzed computationally until the optimum layout is achieved.
In poor countries with very high prevalence of Tuberculosis (TB), like South Africa, there are good examples of buildings that uses natural ventilation, but these are standardized buildings that gets tested over and over and are then rebuilt in different places in the country, especially in rural areas where maintenance of HVAC equipment is a challenge.
David Boshoff
Executive Mechanical Coordinator